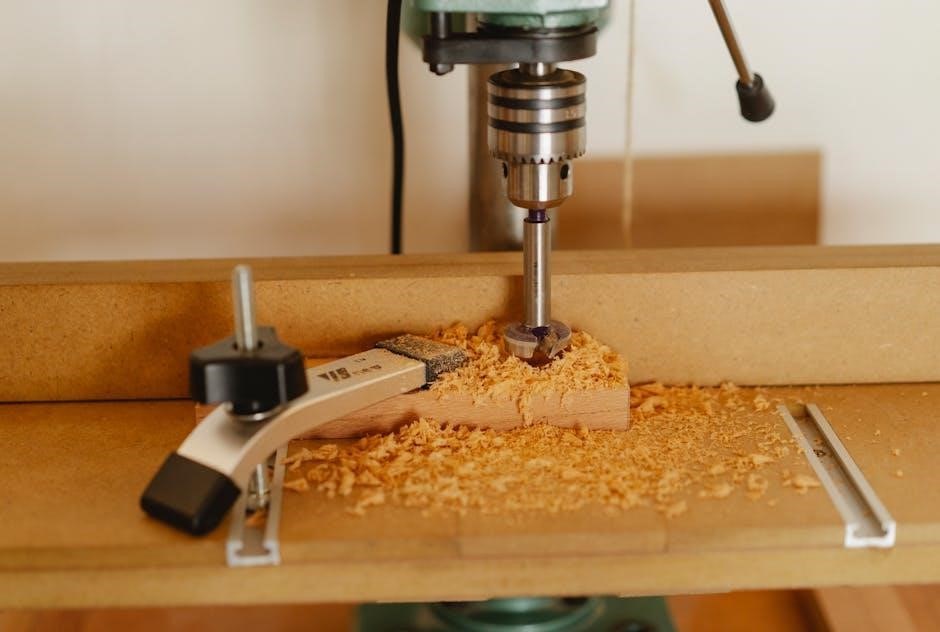
manual press
A manual press machine is a versatile, hand-operated device designed for precision pressing, cutting, and shaping materials like metal, leather, and ceramics. Widely used across industries, it offers simplicity, portability, and cost-effectiveness for small-scale operations and DIY projects.
Overview of Manual Press Technology
Manual press technology involves the use of hand-operated machines designed to apply controlled force for pressing, shaping, or cutting materials. These machines typically feature a simple mechanical or hydraulic system, allowing users to exert precise pressure through a lever or handle. Common components include a C-frame, ram, and base plate, which provide stability and alignment. Manual presses are widely used in crafting, small-scale manufacturing, and DIY projects due to their portability, ease of use, and cost-effectiveness. They are ideal for tasks requiring low to moderate force, such as cutting leather, shaping ceramics, or assembling small parts.
Historical Development and Modern Applications
Manual press machines trace their origins to early industrial tools used for shaping and assembling parts. Over time, their design evolved to incorporate hydraulic systems, enhancing efficiency. Today, these machines are integral in various industries, including manufacturing, crafting, and DIY projects. Modern applications range from cutting leather and ceramics to pressing intricate assemblies. Their versatility and precision make them indispensable for small-scale production and specialized tasks, blending traditional mechanics with contemporary innovations to meet diverse operational needs across the globe.
Applications Across Industries
Manual press machines are widely used in manufacturing, crafting, and DIY projects for precision cutting, shaping, and assembling materials like leather, metal, and ceramics, offering versatility and portability.
Role in General Industry and Manufacturing
In general industry and manufacturing, manual press machines play a crucial role in precision tasks such as cutting, shaping, and assembling materials like metal and leather. Their portability and ease of use make them ideal for small-scale production and workshops. These machines are often used for pressing fittings, removing and installing components, and performing intricate assembly tasks. Their reliability and low maintenance requirements ensure they remain essential tools for industries requiring flexibility and accuracy in daily operations. Additionally, they support ergonomic workflows, enhancing productivity without compromising on quality or safety standards.
Use in Craft and Small-Scale Production
Manual press machines are indispensable in craft and small-scale production, offering precision and versatility for detailed tasks. They are widely used in leatherworking, DIY projects, and small workshops for cutting, shaping, and assembling materials. Craftsmen rely on these machines for tasks like leather die-cutting, embossing, and creating custom designs. Small businesses also utilize them for producing limited quantities of specialized products, such as handmade jewelry or ceramic molds. Their portability and ease of operation make them ideal for artisans and hobbyists, enabling efficient and high-quality outcomes in creative and small-scale manufacturing processes.
Adoption in Hobbyist and DIY Projects
Manual press machines have gained popularity among hobbyists and DIY enthusiasts due to their ease of use and versatility. They enable individuals to craft custom items like buttons, jewelry, and leather goods with precision. DIYers often use these machines for small-scale manufacturing, such as making vitamin or herb tablets, creating personalized designs, or shaping materials like ceramics and metal. Their compact size and manual operation make them ideal for home workshops, allowing hobbyists to explore creative projects without the need for advanced machinery, fostering innovation and self-sufficiency in various crafting endeavors.
Components of a Manual Press
A manual press typically consists of a sturdy C-frame, a movable ram, an operating lever, and a base fixture. These components work together to exert controlled force.
Key Mechanical Parts and Their Functions
The core components of a manual press include a C-frame, which provides structural stability, and a ram that delivers the pressing force. The lever is used to amplify manual effort, transferring it to the ram. A base fixture holds the workpiece in place, ensuring alignment. Some models feature a hydraulic cylinder and pump for smoother operation. These parts work together to enable precise control over the pressing process, making manual presses ideal for tasks requiring accuracy and moderate force. The design emphasizes simplicity, durability, and ease of use, catering to various industrial and craft applications.
Material and Construction Considerations
Manual press machines are typically constructed from durable materials like heavy cast iron or aluminum to ensure stability and longevity. The C-frame design provides structural rigidity, while components such as steel platens or ceramic surfaces enhance heat conductivity and resistance. Hydraulic models often feature stainless steel cylinders for corrosion resistance and smooth operation. The choice of materials depends on the intended application, with heavier-duty presses using thicker, high-strength alloys. Proper construction ensures minimal vibration and consistent performance, making these machines suitable for both industrial and craft applications. Regular maintenance of these components is essential for optimal functionality and extended lifespan.
Advantages and Disadvantages
Manual press machines offer precision, cost-effectiveness, and portability, ideal for small-scale tasks. However, they lack scalability for large production and require manual effort, limiting efficiency in high-volume applications.
Benefits for Precision and Control
Manual press machines excel in delivering precision and control, making them ideal for intricate tasks. Their mechanical simplicity allows operators to apply exact pressure, ensuring consistent results. This level of control is particularly valuable in craft production and small-scale manufacturing where detail matters. Additionally, manual presses are often used in laboratories and workshops for precise assembly and pressing operations. The ability to adjust force manually minimizes material waste and ensures high-quality output, especially in applications like cutting leather or shaping ceramics. This precision makes manual presses indispensable for specialized, low-volume tasks where accuracy is paramount.
Limitations in Large-Scale Production
Manual press machines are less efficient in large-scale production due to their reliance on manual operation, which limits output speed and volume. Unlike automated systems, they require operator input for each cycle, making them time-consuming for high-volume tasks. Additionally, their smaller capacity and lack of automation make them unsuitable for mass production environments where rapid throughput is essential. While they excel in precision and control for small-scale applications, their limitations in scalability and productivity make them less practical for industrial settings requiring high efficiency and consistent large-volume output.
Evolution of Manual Press Technology
Manual press technology has evolved from basic mechanical designs to incorporate hydraulic systems, digital controls, and durable materials, enhancing precision and versatility for modern applications.
From Traditional Designs to Modern Innovations
Manual press machines have transitioned from basic mechanical frameworks to advanced hydraulic and digital systems, offering enhanced precision and efficiency. Modern designs feature ergonomic levers, adjustable ram heights, and durable materials like steel and aluminum, ensuring longevity. Innovations such as electronic monitors and servo-operated controls enable intricate press-fit assemblies, while models like the ManualPress 307/3000 System integrate seamlessly into manufacturing cells. These advancements have expanded the machines’ applications, from crafting leather goods to producing tablets, making them indispensable tools for both industrial and small-scale production environments.
Maintenance and Care
Regular cleaning, lubrication of moving parts, and inspection of hydraulic systems ensure optimal performance. Follow service manuals for specific maintenance routines to extend machine longevity and reliability.
Best Practices for Longevity
Regular cleaning and lubrication of moving parts are essential to ensure smooth operation. Inspect hydraulic systems and components for wear and tear. Always follow the manufacturer’s service manual for specific maintenance routines. Store the machine in a dry, cool place to prevent rust and corrosion. Avoid overloading the press beyond its capacity to maintain performance and durability. Schedule periodic professional inspections to address any potential issues early. Proper care extends the lifespan and ensures consistent reliability of the manual press machine.
Manual vs. Automated Press Machines
Manual presses offer cost-effectiveness and simplicity, ideal for small-scale tasks. Automated presses provide higher speed and consistency, better suited for large-scale production. Each has unique trade-offs in efficiency and cost.
Comparing Efficiency and Cost
Manual presses excel in small-scale, precise tasks, offering lower upfront costs and portability, making them ideal for workshops and DIY projects. Automated presses, while more expensive initially, provide higher efficiency and consistency for large-scale production, reducing labor costs over time. Manual presses require more operator involvement, whereas automated presses minimize human effort but demand significant initial investment and maintenance. The choice between them hinges on production scale, budget, and specific requirements, with each offering unique advantages in different industrial contexts.
Safety Guidelines
- Always wear protective gear, including gloves and safety glasses, when operating manual presses.
- Ensure the machine is stable on a flat surface to prevent accidents.
- Avoid loose clothing that could get caught in moving parts.
- Use correct dies and tools for the task to maintain control.
- Follow the manufacturer’s manual for proper operation and maintenance.
Operating Precautions and Safety Measures
Operating a manual press machine requires careful attention to safety to prevent accidents and ensure efficient performance.
- Always wear protective gear, including gloves and safety glasses, to protect against flying debris or mechanical hazards.
- Ensure the machine is placed on a stable, flat surface to avoid tipping or uneven operation.
- Keep loose clothing or long hair tied back to prevent entanglement with moving parts.
- Use properly aligned dies and tools to maintain control and avoid misalignment-related incidents.
- Never operate the machine while fatigued or distracted, as this can lead to loss of control.
- Follow the manufacturer’s instructions for load limits and operation to prevent overloading or damage.
- Regularly inspect the machine for wear and tear, and perform routine maintenance to ensure optimal function.
By adhering to these precautions, users can minimize risks and achieve safe, effective results when using manual press machines.
Types of Manual Press Machines
Manual press machines vary in design, including hydraulic, mechanical, and arbor presses, each suited for specific tasks like cutting, shaping, and assembling materials with precision.
Different Models and Their Specializations
Manual press machines come in various models, each tailored for specific tasks. Hydraulic presses are ideal for heavy-duty applications like cutting thick materials or pressing metal components. Arbor presses are specialized for precise hole punching and riveting, often used in metalworking. Bench presses are compact and versatile, suitable for small-scale operations like leather cutting or DIY crafts. Additionally, there are die-cutting presses for shaping foam and fabric, and tablet presses for creating pills or vitamins. Each model is designed to cater to different industries, offering unique functionalities that enhance productivity and accuracy in their respective fields.
Manual press machines remain versatile tools, offering precision and adaptability across industries. Their enduring relevance lies in their ability to innovate while maintaining simplicity, ensuring continued demand in modern manufacturing.
Future Prospects and Industry Trends
Manual press machines are expected to evolve with advancements in smart technology, offering enhanced precision and efficiency. Integration with IoT for real-time monitoring is anticipated, while ergonomic designs will gain prominence. Customization options, such as interchangeable dies, will cater to niche markets. The rise of hybrid models blending manual and automated features is forecasted to meet diverse industrial demands. Additionally, eco-friendly materials and energy-efficient designs are likely to become standard, aligning with global sustainability trends. As industries grow, manual presses will remain vital, adapting to modern needs while retaining their hallmark simplicity and reliability.