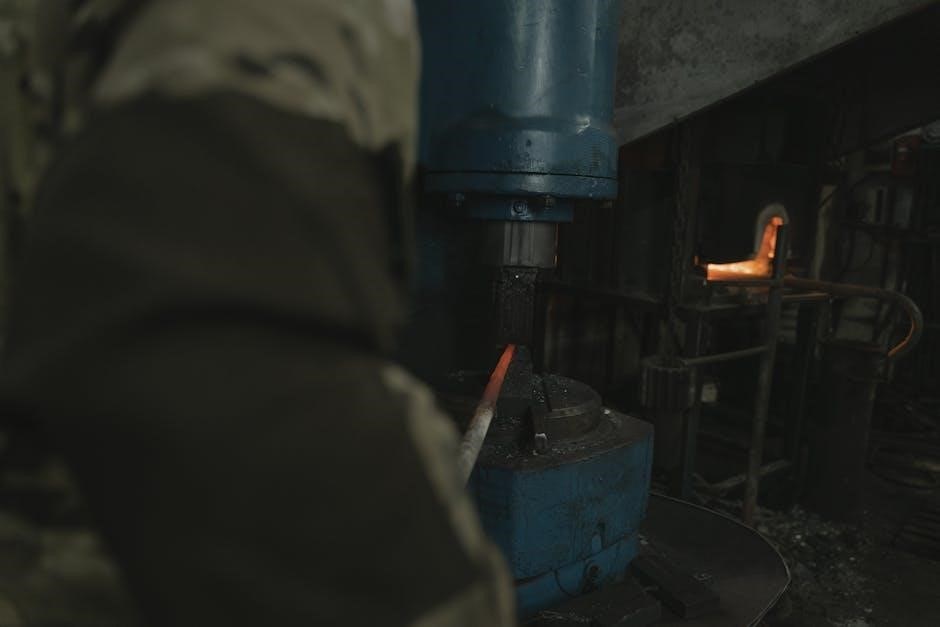
milling machine manuals
Milling machine manuals are crucial for safe and efficient operation. They provide detailed guidance on setup, operation, maintenance, and troubleshooting. Essential for maximizing productivity and ensuring machine reliability.
Overview of Milling Machines
Milling machines are versatile machine tools used to shape materials by removing material via rotating cutters. They enable precise machining of various shapes, from simple to complex geometries. These machines are essential in manufacturing, offering high accuracy and efficiency. Milling machines can operate on multiple axes, with options like vertical, horizontal, and universal configurations. They are widely used in industries such as automotive, aerospace, and electronics. The process involves guiding a cutting tool into the workpiece to achieve desired dimensions and finishes. Milling machines are adaptable to different materials, including metals, plastics, and composites, making them indispensable for modern manufacturing needs.
Importance of Manuals for Safe and Efficient Operation
Milling machine manuals are essential for ensuring safe and efficient operation. They provide detailed instructions on proper setup, usage, and maintenance, reducing the risk of accidents. Manuals outline safety precautions, such as wearing personal protective equipment and using machine guards. They also guide operators in troubleshooting common issues, minimizing downtime. Adhering to manual guidelines ensures optimal performance and extends machine lifespan. Ignoring manual instructions can lead to unsafe conditions and equipment damage. Manuals are critical for both novice and experienced operators, serving as a comprehensive resource for maximizing productivity while maintaining workplace safety. They are indispensable for compliance with industrial standards and best practices.
Types of Milling Machines
Milling machines vary in design, with vertical, horizontal, universal, and CNC types. Each offers unique capabilities, ensuring versatility for diverse machining tasks and precision requirements across industries.
Vertical Milling Machines
Vertical milling machines, like the Bridgeport-style, are widely used for precision machining. They utilize a vertical spindle to hold cutting tools, enabling operations like face milling and drilling. These machines excel at producing flat surfaces and are commonly found in workshops due to their versatility and ease of use. The vertical orientation allows for efficient material removal and precise control over the workpiece. They are particularly effective in industries such as automotive and aerospace for manufacturing components requiring accurate finishes. Routine maintenance, such as spindle lubrication and tool alignment, ensures optimal performance and extends machine longevity.
Horizontal Milling Machines
Horizontal milling machines are designed with a horizontal spindle orientation, making them ideal for heavy-duty machining tasks. They are commonly used for operations like gear cutting and large component production. These machines often feature tilting tables to accommodate complex workpieces. The horizontal design allows for efficient material removal and precise control over cutting tools. Horizontal milling machines are widely used in industries such as automotive and machinery manufacturing. They excel at producing intricate and large-scale parts with high accuracy. Regular maintenance, including spindle alignment and tool sharpening, ensures optimal performance. Their robust construction and versatility make them a cornerstone in many industrial workshops, enabling precise and efficient machining processes.
Universal Milling Machines
Universal milling machines are highly versatile tools capable of performing both vertical and horizontal milling operations. Their adjustable spindle heads allow for a wide range of machining tasks, including face, slot, and angular milling. These machines are ideal for complex workpieces requiring multiple operations in a single setup. Universal milling machines are widely used in precision engineering and prototyping due to their adaptability. They often feature tilting tables and variable speed controls, enabling precise cuts and intricate shapes. Regular maintenance, such as lubricating the axes and calibrating the spindle, ensures optimal performance. Their versatility and precision make them indispensable in workshops and industries requiring diverse machining capabilities, allowing for efficient and accurate production of complex components.
CNC Milling Machines
CNC milling machines are advanced, computer-controlled tools that automate machining processes. They use programmed instructions to execute precise cuts, ensuring high accuracy and consistency. These machines are ideal for complex geometries and large-scale production. Equipped with multiple axes, CNC milling machines can perform tasks like drilling, tapping, and profiling. They are widely used in industries such as aerospace, automotive, and electronics. Regular maintenance, including software updates and spindle calibration, is essential for optimal performance. CNC milling machines offer superior precision, efficiency, and adaptability, making them indispensable in modern manufacturing. Their ability to handle diverse materials and intricate designs ensures high-quality output, meeting the demands of precision engineering and industrial applications.
Key Components of a Milling Machine
A milling machine includes a spindle holding the cutter, a worktable for fixturing the workpiece, axes for movement, and a control panel for programming and operation.
Spindle and Cutter
The spindle is a critical component of a milling machine, rotating the cutter at high speeds to remove material from the workpiece. It is typically aligned with the machine’s axes. The cutter, attached to the spindle, is available in various types, such as end mills, face mills, and slotting cutters, each designed for specific operations. Proper alignment and balance of the spindle and cutter are essential for accurate machining. Regular maintenance, including lubrication and tool inspection, ensures optimal performance. The spindle’s speed and the cutter’s material, such as carbide or high-speed steel, are selected based on the workpiece material and desired finish. This combination enables precise and efficient machining operations across various applications. Always refer to the manual for specific spindle and cutter configurations and maintenance schedules to ensure longevity and accuracy. Proper setup and care are vital for achieving desired results and preventing damage to the machine or workpiece.
Worktable and Axes
The worktable is a fundamental component of a milling machine, serving as the platform for securing and positioning the workpiece. It moves along the X, Y, and Z axes, enabling precise machining operations. The table’s surface is typically made of cast iron for durability and features T-slots for clamping workpieces securely. The axes are labeled based on their movement directions: X (left-right), Y (front-back), and Z (up-down). Manual or power-fed movement options allow for flexibility in machining. Proper alignment and lubrication of the table and axes are essential for smooth operation. Regular maintenance ensures accuracy and prevents wear. Always refer to the manual for specific instructions on adjusting and maintaining the worktable and axes to achieve optimal machining results. Proper setup is critical for ensuring precise and repeatable operations. The worktable and axes are the backbone of milling machine functionality.
Control Panel and Programming
The control panel is the interface for operating the milling machine, housing buttons and displays for setting parameters. It allows users to input speeds, feeds, and coordinates. Modern machines feature CNC (Computer Numerical Control) systems, enabling precise automation. Programming involves creating G-code or using CAM software to define machining operations. The control panel also includes emergency stops and reset buttons for safety. Proper programming ensures accurate and efficient machining. Regular updates and calibration are necessary for optimal performance. Always refer to the manual for specific programming instructions and safety protocols. Understanding the control panel and programming is essential for mastering milling operations and achieving desired results. Proper training is recommended for complex programming tasks;
Milling Operations Explained
Milling operations involve cutting and shaping materials using rotating tools. Common processes include face, slot, and end milling. These operations create precise features and surfaces efficiently.
Face Milling and Slot Milling
Face milling involves cutting the face or surface of a workpiece to create a flat or squared finish. It uses face mills with multiple cutting teeth, ensuring efficient material removal and smooth surfaces. This method is ideal for producing large, flat areas quickly and is commonly used in automotive and aerospace industries for components like engine blocks and aircraft panels.
Slot milling focuses on creating slots or grooves in a workpiece. It employs slotting cutters for precision and is used for keyways, gears, and intricate designs. Slot milling is efficient for groove creation but requires careful chip evacuation. Its adaptability to various materials makes it essential for crafting precise, well-defined slots in industrial applications.
End Milling and Plunge Milling
End milling is a versatile machining process that involves removing material from the end of a workpiece. It uses end mills, such as ball nose or flat end mills, to create contours, slots, or complex shapes. This technique is widely used in industries like aerospace and automotive for crafting intricate components such as gears and molds. Its precision and adaptability make it ideal for profiling and slot cutting, though challenges like tool deflection must be managed.
Plunge milling involves directly inserting a cutting tool into the workpiece to create pockets, holes, or deep features. It is efficient for tasks requiring significant material removal and is commonly used in mold and die manufacturing. Proper tool selection and chip evacuation are critical to avoid complications, but the method excels in producing deep, precise features for various industrial applications.
Side Milling and Thread Milling
Side milling is a process where a side milling cutter removes material from the side of a workpiece. This operation is commonly used to create flat surfaces, slots, and pockets. The cutting tools teeth engage the workpiece from the side, producing a smooth and precise finish. Side milling is versatile and applicable to various materials, including metal, plastic, and wood. It is employed in manufacturing processes such as creating keyways, grooves, or shaping complex contours. The efficiency of side milling makes it an integral part of industries like aerospace, automotive, and general machining, contributing to the production of high-quality components.
Thread milling is a machining process used to produce threads on a workpiece. Unlike traditional threading methods, such as tapping, thread milling employs a milling cutter to create internal or external threads. This method is known for its accuracy, flexibility, and ability to handle various thread profiles. Thread milling is widely used in industries manufacturing screws, bolts, and other threaded components, offering advantages such as improved tool life and the ability to produce threads in challenging materials. This technique is essential for ensuring precise and durable threaded connections in machinery and mechanical systems.
Safety Guidelines and Precautions
Always wear personal protective equipment, ensure machine guards are in place, and familiarize yourself with emergency stops. Proper safety practices prevent accidents and ensure smooth operations. Adhere strictly to manual guidelines.
Personal Protective Equipment
Wearing appropriate personal protective equipment (PPE) is essential when operating a milling machine. Safety glasses or goggles protect eyes from flying debris, while a face mask prevents inhalation of dust and particles. Hearing protection, such as earplugs or earmuffs, is crucial due to the machine’s high noise levels. Steel-toe boots or safety shoes guard against heavy objects, and gloves provide grip and prevent cuts. Ensuring all PPE is worn reduces injury risks and enhances safety. Always follow the manual’s recommendations for specific PPE requirements based on the operation being performed. Proper gear ensures a safer working environment and prevents potential hazards.
Machine Guarding and Emergency Stops
Machine guarding is a critical safety feature that prevents accidental contact with moving or hazardous parts of the milling machine. Guards are designed to protect operators from flying debris, sharp edges, and rotating components. Emergency stops are essential for immediately halting machine operation in case of an unexpected issue or hazard. These stops should be easily accessible and clearly marked. Proper installation and maintenance of guards and emergency stops ensure compliance with safety standards. Always engage the emergency stop when servicing or adjusting the machine. Regularly inspect guards and emergency systems to ensure they function correctly. These measures significantly reduce the risk of accidents and injuries during milling operations.
Maintenance and Troubleshooting
Regular maintenance ensures optimal performance and longevity of milling machines. Inspect and clean components, check for wear, and perform timely repairs. Address common issues promptly using manual guidelines.
Routine Maintenance Tasks
Regular lubrication of moving parts and thorough cleaning of the worktable and guides are essential. Inspect spindle alignment and tool holders for wear, ensuring precision cutting. Check coolant systems for proper function and maintain hydraulic fluid levels. Routinely sharpen or replace cutting tools to prevent wear and tear. Schedule periodic spindle bearing checks and motor maintenance to avoid unexpected downtime. Ensure all machine guards are secure and emergency stops function correctly. Adhere to manufacturer guidelines for part replacements and software updates. Proper maintenance extends machine life, enhances accuracy, and ensures safe operation, minimizing costly repairs and downtime.
Common Issues and Solutions
Common milling machine issues include tool deflection, vibration, and spindle misalignment, which can lead to inaccurate cuts. Worn-out cutting tools often cause poor surface finishes and dimensional errors. Solutions involve regular tool inspections and replacements. Vibrations can be minimized by ensuring proper workpiece clamping and spindle alignment. Misalignment issues require recalibration or professional adjustment. Coolant system malfunctions can cause overheating, addressed by checking fluid levels and pump functionality. Additionally, chip buildup can interfere with operation, necessitating frequent cleaning. Proper lubrication of moving parts and timely replacement of worn components prevent downtime. Addressing these issues promptly ensures optimal performance and extends machine lifespan.
Milling machine manuals are indispensable resources for operators, ensuring safe, efficient, and precise machining. They provide comprehensive guidance on setup, operation, and maintenance, helping users unlock the full potential of their machines. By adhering to the instructions and troubleshooting tips outlined in these manuals, operators can minimize downtime and optimize productivity. Whether addressing common issues or mastering advanced techniques, milling machine manuals serve as a cornerstone for achieving professional results. Their importance cannot be overstated, as they empower users to handle diverse milling operations with confidence and accuracy, ultimately driving success in manufacturing and engineering projects.