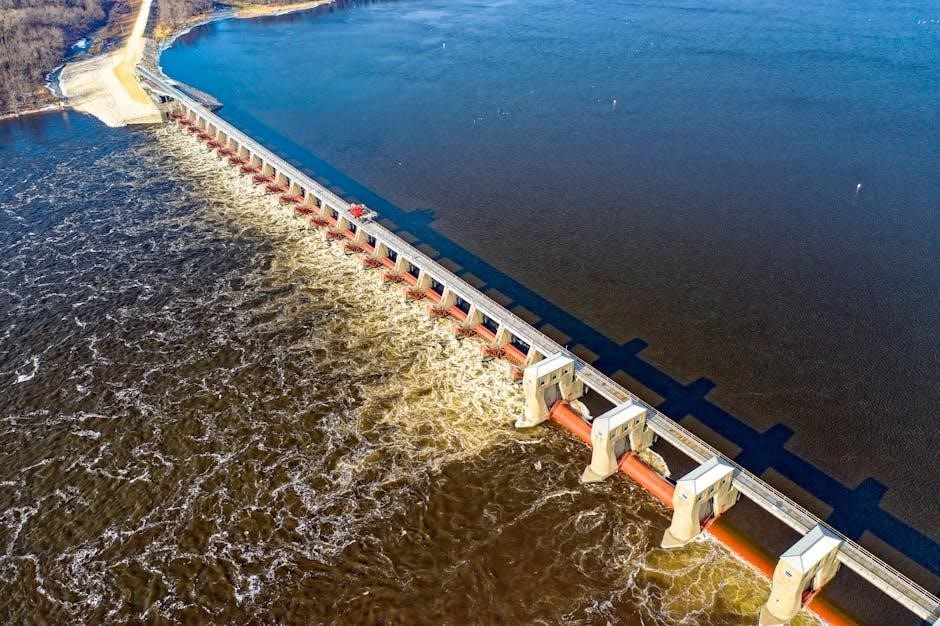
bleeding hydraulic system on a ghs system pdf
Hydraulic systems in GHS operate by transmitting energy through pressurized fluid‚ enabling precise control in applications like aviation and construction․ Components include pumps‚ actuators‚ and valves‚ ensuring high efficiency and reliability․ GHS guidelines ensure safe handling of hazardous hydraulic fluids‚ emphasizing proper classification‚ labeling‚ and safety protocols․ Bleeding is critical for maintaining system integrity by removing air and contaminants‚ aligning with GHS standards for environmental and workplace safety․ Regular maintenance ensures optimal performance‚ preventing damage and extending system lifespan․
Overview of Hydraulic Systems
Hydraulic systems are mechanical arrangements that operate by transmitting energy through pressurized fluid‚ enabling precise control over motion and force․ They consist of key components such as pumps‚ actuators‚ control valves‚ and fluid lines‚ which work together to achieve high power-to-weight ratios and reliability․ Widely used in aviation‚ construction‚ and industrial machinery‚ these systems rely on fluid integrity for optimal performance․ In GHS-compliant applications‚ hydraulic systems handle hazardous fluids‚ requiring strict safety measures to prevent accidents and environmental contamination․ Their efficiency and safety depend on proper maintenance and adherence to GHS guidelines․
Role of GHS in Hydraulic System Maintenance
GHS plays a vital role in hydraulic system maintenance by ensuring the safe handling of hazardous hydraulic fluids․ It provides standardized guidelines for classifying and labeling chemicals‚ crucial for maintaining system integrity․ GHS helps prevent contamination and ensures compliance with safety regulations during maintenance tasks like bleeding․ By adhering to GHS‚ technicians can identify potential hazards associated with hydraulic fluids‚ such as toxicity or flammability‚ and take appropriate precautions․ This compliance enhances workplace safety‚ protects the environment‚ and ensures reliable system performance․ Regular training on GHS standards is essential for technicians to understand hazard communication and maintain operational safety․
Importance of Bleeding Hydraulic Systems
Bleeding hydraulic systems is essential for removing air and contaminants‚ ensuring optimal performance‚ preventing damage‚ and aligning with GHS safety and environmental standards․
Why Bleeding is Critical for System Efficiency
Bleeding hydraulic systems is vital for removing trapped air and contaminants‚ ensuring smooth operation and preventing reduced performance․ Air pockets cause pressure drops‚ overheating‚ and fluid degradation‚ which can lead to component damage․ Proper bleeding maintains fluid integrity‚ essential for high-pressure systems․ It prevents efficiency loss‚ extends equipment lifespan‚ and aligns with GHS guidelines for safe chemical handling․ Regular bleeding ensures reliable performance‚ especially in critical applications like aviation‚ where system failure can have severe consequences․ It is a cornerstone of hydraulic system maintenance․
Consequences of Not Bleeding the System
Failing to bleed hydraulic systems allows air to remain‚ reducing system efficiency and causing increased stopping distances due to compressible air in the brake system․ This can lead to serious safety hazards‚ including brake failure and personal injury․ Air pockets also cause overheating‚ fluid degradation‚ and damage to components․ Neglecting bleeding can result in system malfunction‚ increased wear on parts‚ and reduced overall performance․ In critical applications like aviation‚ this can lead to catastrophic failures‚ emphasizing the importance of regular bleeding to maintain reliability and safety․
The Role of GHS in Hydraulic System Safety
GHS ensures safe handling of hazardous hydraulic fluids through standardized classification and labeling‚ promoting workplace safety and environmental protection by providing clear hazard communication and safety protocols․
GHS Guidelines for Hydraulic Fluid Handling
GHS guidelines ensure the safe management of hydraulic fluids classified as hazardous․ Proper labeling‚ storage‚ and handling procedures are mandated to minimize risks․ Safety Data Sheets (SDS) provide detailed information on handling‚ storage‚ and emergency procedures․ Personnel must use personal protective equipment (PPE) and follow spill prevention measures․ Training on GHS standards is essential for understanding hazard communication and safe practices․ Compliance with these guidelines protects both workers and the environment‚ ensuring the safe operation and maintenance of hydraulic systems․ Adherence to GHS is critical for maintaining a safe working environment․
Hazard Classification and Labeling in Hydraulic Systems
Hazard classification and labeling are critical under GHS to ensure safe handling of hydraulic fluids․ Hydraulic systems often use hazardous fluids categorized by health‚ physical‚ and environmental hazards․ These fluids are labeled with standardized symbols and phrases‚ providing clear hazard communication․ Proper labeling helps identify risks‚ such as flammability or toxicity‚ guiding safe handling practices․ Accurate classification ensures compliance with international standards‚ reducing risks to workers and the environment․ This systematic approach enhances safety and regulatory compliance during hydraulic system maintenance and operation․
Preparing for Hydraulic System Bleeding
Preparation involves gathering tools‚ depressurizing the system‚ and cleaning the area to minimize contamination․ Check fluid levels‚ wear PPE‚ and ensure compliance with GHS guidelines․
Tools and Equipment Needed
Bleeding a hydraulic system requires specific tools‚ including wrenches‚ pressure gauges‚ and fluid reservoir keys․ Essential items also include hydraulic fluid‚ a clean container for drainage‚ and a service manual․ Ensure all tools are compatible with the system to avoid damage․ Use protective equipment like gloves and goggles for safety․ A clean work area minimizes contamination risks․ Proper lighting and a drain pan are also recommended․ Always refer to the system manual for specific tool requirements and follow GHS guidelines for handling hydraulic fluids to ensure safety and compliance during the bleeding process․
Depressurizing the System
Depressurizing the hydraulic system is essential before bleeding to ensure safety and prevent sudden pressure releases․ Start by turning off the power supply and engaging the system’s safety locks․ Use approved valves or controls to gradually release pressure from the system․ Refer to the system manual for specific depressurization procedures․ Always wear PPE‚ such as gloves and safety glasses‚ to protect against potential fluid leaks․ Ensure the system is at ambient pressure before proceeding with bleeding․ This step aligns with GHS guidelines for safe handling of hydraulic systems and hazardous materials․
GHS Safety Measures During Preparation
Adhering to GHS guidelines is crucial during hydraulic system preparation to ensure safe handling of hazardous materials․ Proper labeling and storage of hydraulic fluids are essential to prevent accidental exposure․ Always wear personal protective equipment (PPE)‚ including gloves and goggles‚ to protect against chemical splashes․ Ensure the workspace is well-ventilated to avoid inhalation of hazardous fumes․ Follow GHS guidelines for safe handling procedures to minimize the risk of spills and contamination․ Properly dispose of waste materials according to environmental regulations to maintain compliance and protect the environment․
Executing the Bleeding Process
Executing the bleeding process involves loosening bleed valves‚ using a wrench to release air and fluid‚ and monitoring for bubbles to ensure efficient system operation․
Step-by-Step Bleeding Procedure
The bleeding process begins with loosening bleed valves at low points or near actuators․ Open valves slowly to release air and fluid‚ monitoring for bubbles․ Once fluid flows steadily without bubbles‚ tighten the valve․ Repeat for all components‚ ensuring the reservoir remains filled to avoid introducing new air․ Use pressure gauges to verify system pressure after bleeding․ If air pockets persist‚ consult the manual or use specialized tools․ Adhere to GHS guidelines for handling fluids and wear PPE to ensure safety and compliance during the process․
Monitoring for Air and Contaminants
During bleeding‚ monitor the fluid for bubbles‚ which indicate air in the system․ Use a pressure gauge to check system pressure and ensure it reaches the recommended level․ Visually inspect fluid lines and components for signs of contamination or leaks․ Maintain a clean work environment to prevent foreign particles from entering the system․ Regularly check the fluid reservoir level to avoid introducing new air during the process․ Proper monitoring ensures the system operates efficiently and safely‚ aligning with GHS guidelines for hazardous material handling and system maintenance․
Common Challenges During Bleeding
Air locks and fluid leaks are common challenges during bleeding․ Air locks prevent proper fluid flow‚ causing inefficiencies‚ while leaks introduce air‚ compromising system performance and safety․
Identifying and Resolving Air Locks
Air locks in hydraulic systems occur when air pockets trap fluid‚ disrupting flow and efficiency․ Symptoms include spongy pedals or slow system response․ To resolve‚ use specialized tools or sequential bleeding․ Ensure proper venting and purge components thoroughly․ Regular maintenance and GHS compliance minimize air lock risks‚ ensuring safe fluid handling and system reliability․ Prompt resolution prevents overheating and component damage‚ maintaining optimal performance and safety․
Addressing Fluid Leaks
Fluid leaks during bleeding compromise system performance by introducing air and contamination․ Inspect connections‚ seals‚ and components for damage or misalignment․ Tighten loose fittings and replace worn seals․ Use GHS-compliant sealants to prevent further leaks․ Regular inspections and timely repairs are crucial to maintain system integrity․ Neglecting leaks can lead to inefficient bleeding‚ prolonged downtime‚ and potential component damage․ Addressing leaks promptly ensures successful bleeding outcomes and maintains hydraulic system efficiency and safety‚ aligning with GHS guidelines for hazardous fluid management․
Safety Protocols During Bleeding
Adhering to safety protocols during bleeding ensures hazard control‚ protects against fluid exposure‚ and prevents system damage by following GHS guidelines and using proper protective equipment․
Personal Protective Equipment (PPE)
Wearing appropriate PPE is essential during hydraulic system bleeding to protect against hazardous fluid exposure․ Gloves prevent skin contact with chemicals‚ while safety goggles shield eyes from splashes․ A respirator may be needed for volatile fluids‚ and steel-toe boots protect from heavy tools or fluid spills․ Proper PPE aligns with GHS guidelines‚ ensuring worker safety and minimizing environmental risks․ Always use GHS-compliant equipment and follow safety protocols to handle hazardous materials effectively․
Environmental Protection Measures
Environmental protection is critical during hydraulic system bleeding to prevent chemical spills and contamination․ Proper disposal of waste fluids and materials is essential‚ following local regulations․ Spill containment kits should be on hand to manage accidental leaks‚ protecting soil and water․ Using GHS-compliant storage and labeling ensures fluids are handled safely‚ reducing environmental risks․ Regular training on eco-friendly practices helps minimize ecological impact‚ aligning with GHS standards for sustainable and responsible hydraulic system maintenance․
Best Practices for Hydraulic System Maintenance
Adhere to regular maintenance schedules and GHS guidelines to ensure hydraulic system efficiency and safety․ Proper fluid handling‚ timely inspections‚ and preventive measures minimize downtime and hazards․
Regular Maintenance Schedules
Establishing regular maintenance schedules is essential for hydraulic system longevity․ Plan fluid changes‚ component inspections‚ and bleeding procedures based on usage and manufacturer guidelines․ Consistent monitoring ensures early detection of issues like air locks or leaks․ Adhering to GHS standards during maintenance protects both personnel and the environment from hazardous fluid exposure․ A well-structured schedule minimizes unexpected downtime‚ optimizes system performance‚ and aligns with safety regulations․ Regular checks also help prevent contamination‚ ensuring reliable operation in high-pressure applications․ Compliance with GHS guidelines further enhances workplace safety and environmental compliance‚ making routine maintenance a critical practice․
Ensuring GHS Compliance
Ensuring GHS compliance is vital for safe handling of hydraulic systems․ This involves proper classification‚ labeling‚ and hazard communication of hydraulic fluids․ Technicians must follow GHS guidelines for handling hazardous materials‚ including the use of safety data sheets (SDS) and personal protective equipment (PPE)․ Regular training on GHS standards ensures awareness of chemical hazards‚ such as flammability or toxicity․ Compliance also involves proper storage and disposal of hydraulic fluids to prevent environmental contamination․ By adhering to GHS‚ organizations minimize risks‚ protect workers‚ and maintain regulatory alignment‚ ensuring a safer working environment and operational integrity․
Bleeding hydraulic systems in GHS ensures efficiency‚ safety‚ and compliance․ Proper procedures remove air and contaminants‚ aligning with GHS guidelines to maintain system longevity and operational integrity․
Bleeding hydraulic systems in GHS ensures efficiency by removing air and contaminants‚ aligning with safety guidelines․ GHS emphasizes proper handling of hazardous fluids‚ classification‚ and labeling․ Tools like wrenches and pressure gauges are essential‚ with depressurization and fluid checks critical before bleeding․ Adhering to GHS safety measures prevents environmental harm and workplace injuries․ Addressing challenges like air locks and fluid leaks is vital for optimal performance․ Regular maintenance extends system longevity‚ ensuring reliability and compliance with international standards for safe chemical management․
Importance of Adhering to GHS Guidelines
Adhering to GHS guidelines ensures safe handling of hazardous hydraulic fluids‚ protecting workers and the environment․ Proper classification‚ labeling‚ and safety data sheets enable clear hazard communication․ Compliance minimizes risks of chemical exposure‚ ensuring workplace safety and regulatory adherence․ GHS alignment maintains system efficiency by preventing contamination during bleeding․ Regular training and adherence to GHS protocols safeguard against accidents and environmental harm‚ promoting sustainable and responsible hydraulic system maintenance practices globally․